Why tolerance is important in manufacturing?
Tolerance is the acceptable range for a physical dimension. Product designers determined this physical dimension based on the form, fit, and function of a part. Tight tolerance standards are set to ensure the delivery of high-quality, safe products to our customers. Obtaining the appropriate tolerance during the manufacturing process is pivotal in determining how well the final product will fit and run in your machinery.
Checking that all tolerances are labeled correctly is important when providing drawings to any engineering department. This small detail can greatly affect any quote you receive.
Even slight differences in tolerance can affect the following:
- Final Cost:
- Requesting tolerances that are tighter than a standard range is very important in certain applications, yet does add a substantial cost to the overall quote.
- Production Times:
- Tighter tolerances require the roll to be worked on across multiple machining centers. Often at a much slower speed to achieve precision grinding.
- Lifespan of Roller:
- Properly machined and fitted rollers will run smoother in day-to-day productions. Thus leading to a longer lifespan of the roller itself.
Seven-tenths of a thousands of an inch may seem like a small difference, but that minor detail can actually mean the difference of several hundred dollars and extra days of machining time. Because of this, it is important to make sure the tolerances on drawings are all accurate. Often times, we see journals coming in with ±0.010 yet the bearing tolerance states +0.0007 / -0.0000 for the entire length of the journal. In this case, we would actually have to manufacture the entire journal to the specified bearing tolerance. Which results in higher costs and longer production times. This could have been avoided simply by including on the original drawing, a notation that states the bearing tolerance is only to be applied to the specified width of the bearing (most are less than 2” wide).
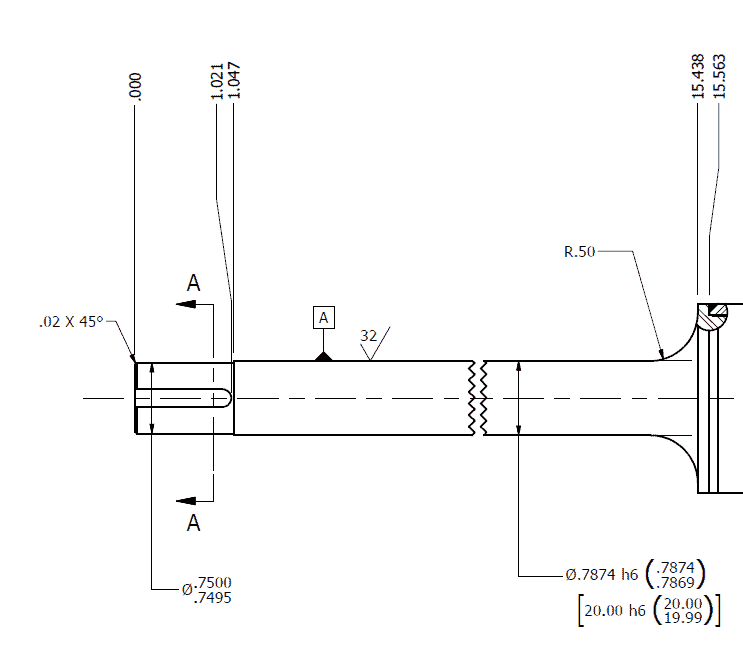
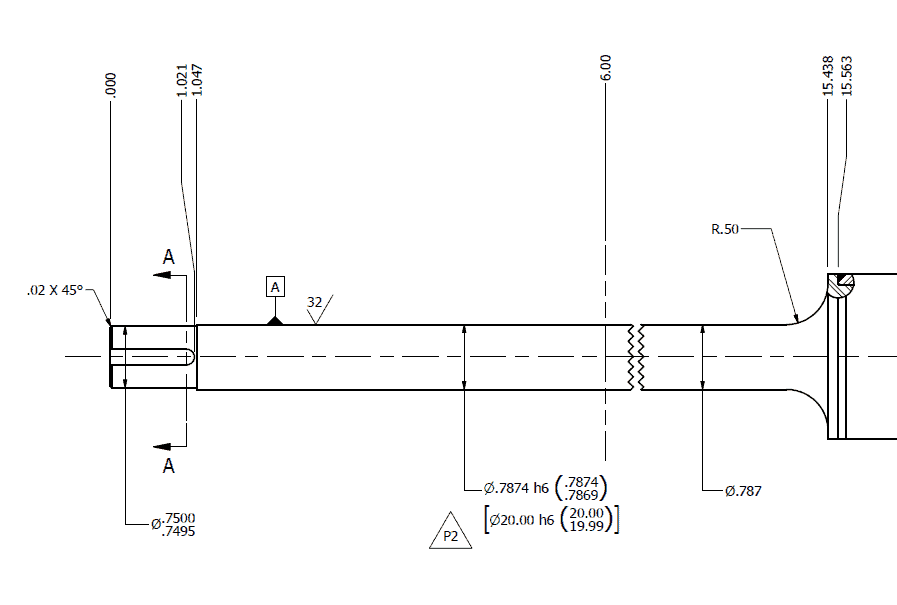
Proper applications of tolerances
While tolerances are important, it is just as important to apply them correctly. The final fit of a roller is important to keep in consideration when determining tolerances. This is how shafts will fit into bearings or bushings, motors into pilot holes, and so on. Depending on your application, you might want a clearance fit to allow for expansion due to heat, a sliding fir for better positioning, or an interference (press) fit for holding capability.
When in doubt, our engineering department is available to answer any questions you may have regarding tolerance standards. Having worked with many different types of rollers across various industries and applications, they are your go-to experts for engineering questions.
Give us a call to talk about tolerancing options with one of our engineering experts!
Contact Us |